CEMENT BLOCK
Solid / Hollow Concrete Blocks
Description
Concrete Block Technology is based on the principle of densification of a lean concrete mix to
Make a regular shaped, uniform, high performance masonry unit. Concrete Block Technology can
be easily adapted to suit special needs of users by modifying design parameters such as mix
proportion, water/cement ratio and type of production system. It is an effective means of utilizing
wastes generated by stone crushers, quarrying and stone processing units. The technology has
high potential in areas where raw materials are easily available. The Concrete Block Technology
Package is a highly profitable business for micro and small scale building material producers and
construction companies.
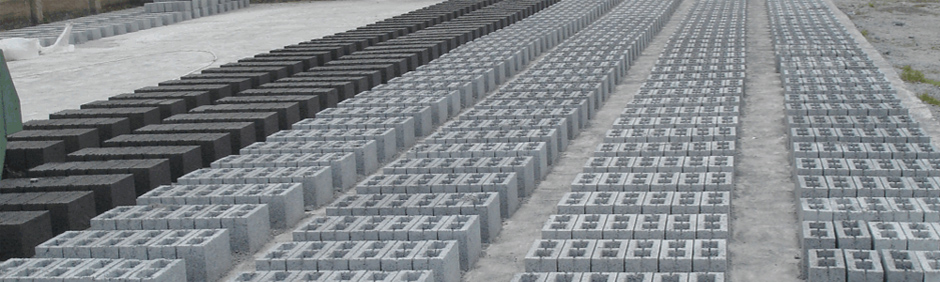
PERFORMANCE SUMMARY
Appearance
Concrete blocks will have a light grey concrete colour, and on close inspection may show a
granular texture depending in the type of aggregate used. Machine production provides even
finish which offers savings on further cement plaster etc. Concrete blocks can be surface
engineered by using pieces of stone or ceramic waste on their face. Another common type is
hollow concrete blocks. They are made with a richer mix, but offer a number of advantages, such
as lighter weight, easier handling and facility for conducting or reinforcement through the
hollows.
Structural Capability
Major advantage of concrete blocks is that their strength can be engineered as per requirement.
Thus making them relatively stronger than masonry with bricks walls by around 15-20%. The
specifications and the characteristics of a concrete block depend on the machine used to
manufacture concrete blocks. The basic raw material is cement, fine aggregate and coarse
aggregate. Very little water is used. This is possible only with mechanized compaction and
vibration and gives the block high quality in spite of the lean mix, which uses very little cement.
These blocks are 4-5 times bigger than burnt bricks; the size of the block or brick used has a
bearing on the strength of the masonry. As the bigger size accounts for reduction in the number of
mortar joints, thereby increasing wall strength. Weight of a concrete block is about 18-19 Kg’s.
High quality machines provide optimum vibration in the mix so that the ratio of cement used can
be reduced substantially without compromising on the strength of the blocks. The machine also
compacts and consolidates the mix so that the blocks are uniform in size and attain desired
physical properties. The blocks are cured for a minimum period of 14 days, before they are ready
to use.
Thermal properties
Concrete blocks have an excellent thermal property, comparable to other masonry blocks. The
cavities in the blocks provide better thermal protection and also do not need external or internal
plastering. The performance of these blocks increases with the increase in the number of hollow
Cores, which may or may not be filled in with some insulating materials.
Sound insulation
Concrete blocks provide an acceptable degree of sound insulation.
Fire and vermin resistance
Concrete blocks will not burn. They are readily incorporated into fire resistant rated construction.
It has no problems of vermin attacks or infestation.
Durability and moisture resistance
They are very popular as a long lasting, low maintenance masonry unit, with good compressive
strengths. They have a general life’s span of about 60yrs although may extend up to 80yrs or
more. They are robust and durable even if wetted. It water absorption is less than 10% of weight
of block, after just 24hrs, and may need a weatherproof coating to keep the moisture out.
Toxicity and Breath-ability
Concrete blocks are inert, non-toxic and not prone to off-gassing of volatile materials.
Sustainability
(Environmental impacts)
Cement contributes maximum to the embodied energy of the product and masonry. Production
and application procedures for concrete blocks have been optimized to maximize efficiency of
cement use. The embodied energy in concrete blocks masonry is 270 MJ/Sqm as against 640
MJ/ Sq.m for brick walls. Therefore concrete blocks, through efficient use of cement, consume less
than 50% of the energy, which is consumed by brick walls.
Build ability, availability and cost
It has been found that concrete blocks enable savings of approx. 8-9% per sq m. of masonry as
compared with burnt bricks. This is primarily because of the savings in mortar and faster
construction speed, both due to the larger block size and also due to the savings in plaster. Size
optimization of concrete blocks also leads to increase in usable internal space, when compared to
conventional fired brick construction. Construction techniques involved is similar to other
masonry units thus easily adaptable. Through decentralized local production it is easily available
through a large number of manufacturers and distributors in most parts of India, in both rural and
urban areas.. Cost is almost equal or lesser than an equivalent number of bricks per sq m. of wall.
Applicability
Concrete blocks have various types like; solid, hollow, paving, tree-guard blocks, and each of
them are available in various shapes and sizes. This vast range of products offers a large market
for application.
• In load bearing structures -low rise residential and office buildings, bungalows, shelter units
for rural housing, highway constructions, institutional buildings, god owns and warehouses etc.
• In frame structures – High rise residential apartments, office buildings, market complexes,
hospitals and hotels etc.
• As ground laying units – interlocking paving blocks for roadside walkways, garden pathways,
curb stones, exhibition grounds, fuel pumping stations, movement corridors, high traffic
movement areas like: bus and train stations etc.
• Specific usage areas: tree guard blocks for roadside and garden tree plantations
Manufacturers